Photo Credit: Prakasit Lalao via Adobe Stock.
What is carbon fiber? Why are supercars made of it?
Carbon-fiber-reinforced polymers are composite materials reserved for the most high-performance vehicles. But why? Simple: Carbon fiber is strong, light, and looks cool.
Are you not satisfied with that simplistic answer most car people just accept? I am with you. I am going to get you up to speed on carbon fiber composites.
My name is Colin Finkle. I am an industrial designer and have designed parts and produced engineering drawings for projects using many different materials for over a decade and a half. I have some experience with carbon fiber; I have toured a factory that makes carbon fiber parts.
Carbon fiber is a composite material used to construct the chassis, bodywork, and some mechanical parts of the ultimate performance vehicles and race cars. Carbon fiber parts are incredibly light while maintaining the strength of steel, aluminum, or fiberglass parts, making carbon fiber the ultimate choice for reducing weight and preserving mechanical performance.
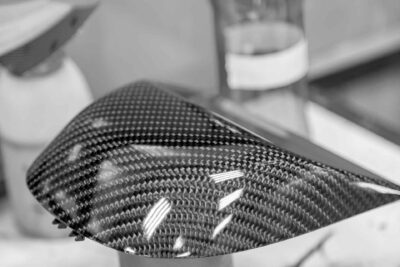
Legendary supercars like the Ferrari, Bugatti Chiron, McLaren P1, and Lamborghini Veneno are primarily made of carbon fiber. Formula 1 cars are constructed from carbon fiber.
Carbon fiber reinforced polymer (CFRP) is what car people mean when people say “carbon fiber” in reference to performance cars. Carbon fiber reinforced polymer is a molded body of polymers with carbon fibers in the middle to add strength.
Carbon fiber reinforced polymer is much like fiberglass but far more robust. Both are composites utilizing a polymer matrix. But fiberglass uses strands of glass, while carbon fiber uses strands of carbon atoms. Diamonds are made of carbon atoms too and it is the hardest material in the world.
Technically, carbon fiber refers to the thin and amazingly strong string of carbon atoms that is the basis of carbon fiber reinforced polymer. It is nearly impossible to make it stretch or snap; in other words, carbon fiber has excellent tensile strength. These carbon fibers are usually woven into a sheet before being cast into the middle of a resin, so the strings and their strength go in all different directions.
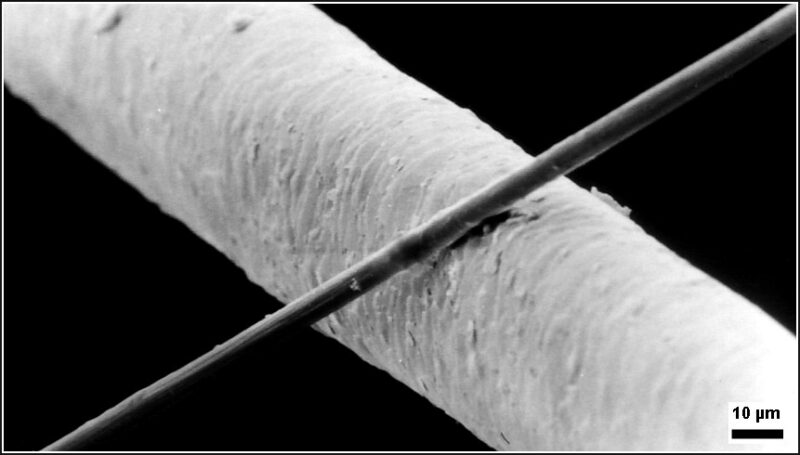
Supercars Made Of Carbon Fiber
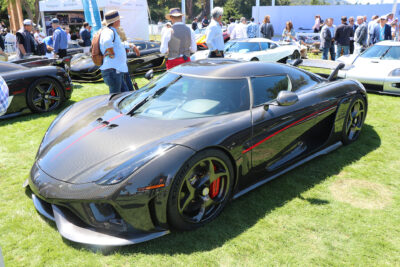
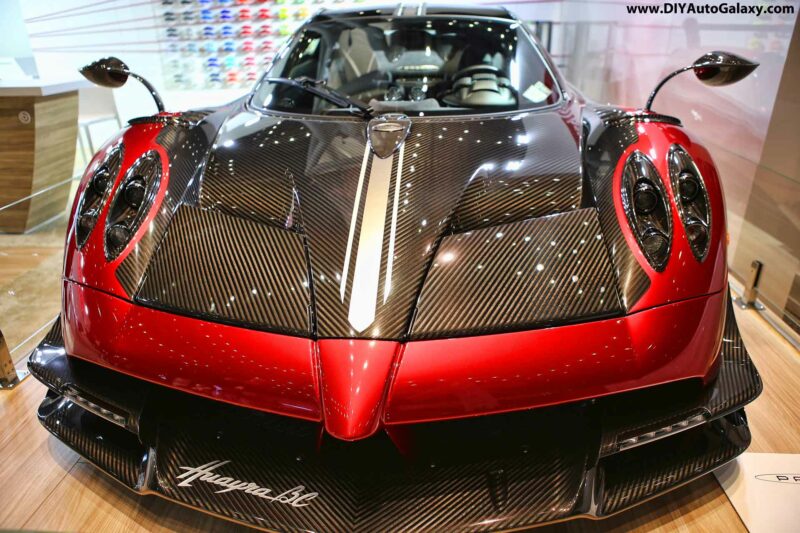
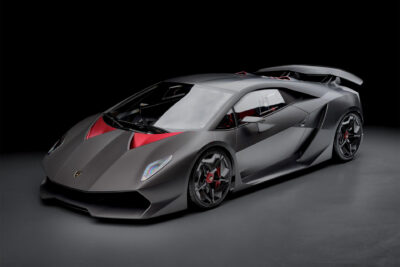
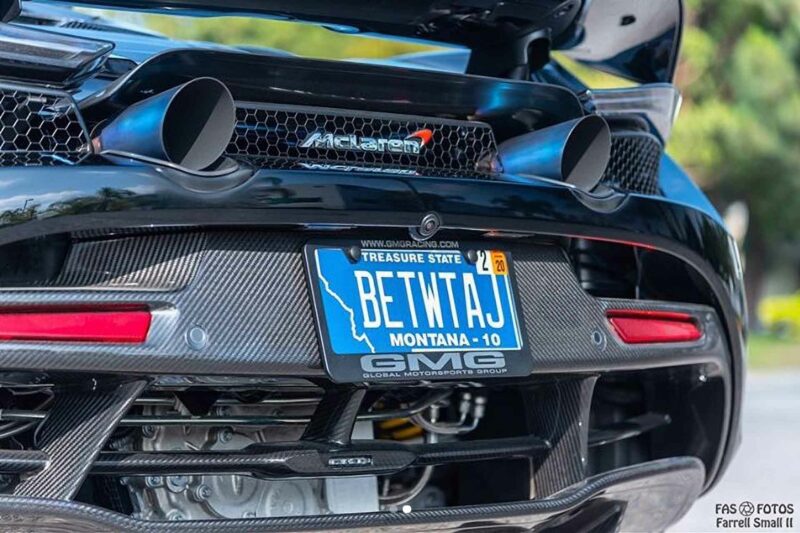
- Aston Martin Valkyrie AMR Pro
- Aston Martin One-77
- BAC Mono
- BMW i8
- Bugatti Bolide
- Bugatti Chiron
- Bugatti Veyron
- Bugatti W16 Mistral
- Ford GT
- Ferrari F50
- Ferrari Enzo
- Ferarri LaFerrari
- Gordon Murray Automotive T50
- Hennessey Venom F5
- Jaguar XJR-15
- Koenigsegg Agera
- Koenigsegg CC850
- Koenigsegg CCR
- Koenigsegg CCX
- Koenigsegg Gemera
- Koenigsegg Jesko
- Koenigsegg Regera
- Koenigsegg Trevita
- Lamborghini Revuelto
- Lamborghini Invencible
- Lamborghini Auténtica
- Lamborghini Countach LPI 800-4
- Lamborghini Essenza
- Lamborghini Sián
- Lamborghini Centenario
- Lamborghini Veneno
- Lamborghini Sesto Elemento
- Lamborghini Aventador
- Lamborghini Reventón
- Lexus LFA
- McLaren 12C
- McLaren 570S
- McLaren 570GT
- McLaren 650S
- McLaren 675LT
- McLaren 720S
- McLaren Artura
- McLaren F1
- McLaren P1
- McLaren Senna
- McLaren Speedtail
- Marcedes-Benz SLR McLaren
- Pagani Huayra R
- Pagani Utopia
- Pagani Zonda
- Porsche Carerra GT
- Porsche 918 Spyder
- Zenvo Aurora
- Zenvo TSR-S
Why is carbon fiber special?
The rare combination of lightweight and strength makes carbon fiber reinforced polymer perfect for supercars, hypercars, jets, rockets, speedboats, and sporting equipment.
A carbon fiber part for a supercar will be much lighter and stiffer than a similar part made out of metal or basic plastic.
The ability to cut weight while maintaining stiffness makes carbon fiber composite essential for high-performance automotive and aerospace applications where every ounce (or gram) of weight reduction counts and performance is non-negotiable.
The carbon fibers provide incredible tensile strength and stiffness, crucial for the structural demands of high-speed vehicles and aircraft. Carbon fiber composite is also resistant to moisture, corrosion, and thermal expansion, making it durable in varying environmental conditions. Carbon fiber can also be made into complex shapes like the body panels of modern supercars.
Carbon fiber is also just cool.
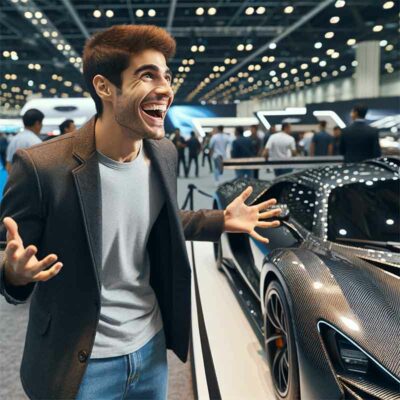
Car guys and gals also think carbon fiber is cool and looks badass. Automotive enthusiasts see carbon fiber as a symbol of no-compromise performance.
“Carbon fiber means performance” is an idea pushed on us by car manufacturers, aftermarket part manufacturers, automotive media, and other enthusiasts.
But here we are; when car people like us see carbon fiber, we know a car is about performance. (Unless it is only for looks.)
Why are supercars made of carbon fiber?
Supercars have parts and chassis made of Carbon Fiber Reinforced Polymer (CFRP) because this material significantly reduces a vehicle’s weight because parts can be small and light while achieving their required strength.
Supercars with carbon fiber monocoques are also more rigid, keeping the chassis from twisting and maintaining the suspension mounting points under extreme acceleration and cornering loads.
The reduced weight and rigidity from using carbon fiber parts have several performance benefits for supercars:
- Improved Acceleration: Lighter cars can move faster with less force, allowing supercars to accelerate more quickly. They can achieve incredible speeds in a matter of seconds.
- Enhanced Braking: A vehicle that is lighter because it is made of carbon fiber takes a shorter distance and time to stop. Lighter cars also put less heat and strain into their brakes when repeatedly used, such as on a racetrack.
- Higher Turning Speeds: Reduced weight improves a car’s ability to handle corners at speed (lateral Gs). Supercars can thus navigate sharp turns and curves more effectively, maintaining speed without losing control.
- Improved Handing: The rigidity of a carbon fiber chassis enhances the handling and agility of a supercar. A rigid body structure ensures the car responds precisely to driver inputs, offering enhanced control and stability, vital at high speeds or during dynamic driving.
- Safety: This structural rigidity of carbon fiber keeps the car from bending under loads and supports the overall durability and safety of the supercar.
Carbon fiber construction has been a fantastic innovation, helping achieve the record-setting performance and handling characteristics we measure in modern supercars.
Uses of Carbon Fiber in Supercars
Supercars often incorporate carbon fiber in various components to leverage its strength, lightweight, and aesthetic appeal. Here’s a list of supercar components that are frequently made from carbon fiber:
- Body Panels: Including hoods, doors, roofs, bumper covers, and trunk lids.
- Monocoque: A carbon fiber monocoque is a type of chassis that uses the passenger compartment and front and rear members as structural components. This structure is found on hypercars and fighter jets.
- Aerodynamic Components: Spoilers, wings, skirts, louvers, fins, and diffusers are often made of carbon fiber to hold up to the extreme aerodynamic load that creates downforce.
- Braces and Brackets: The small structural add-on parts like gussets, mounting arms, and braces are made of carbon fiber.
- Interior Components: Dashboards, center consoles, and door panels are often made of carbon fiber to reduce weight and achieve a high-end look.
- Seats: Racing-style bucket seats made of CFRP are lightweight and only slightly uncomfortable (in my opinion!).
- Wheels: We are now seeing rims made entirely out of carbon fiber.
- Engine Components: This includes air intake systems and engine covers for reduced weight.
- Suspension Components: Parts like upper and lower control arms are made of carbon fiber to reduce unsprung weight, increasing handling performance.
- Mirror Casings: Often made from carbon fiber for a sleek look and reduced weight.
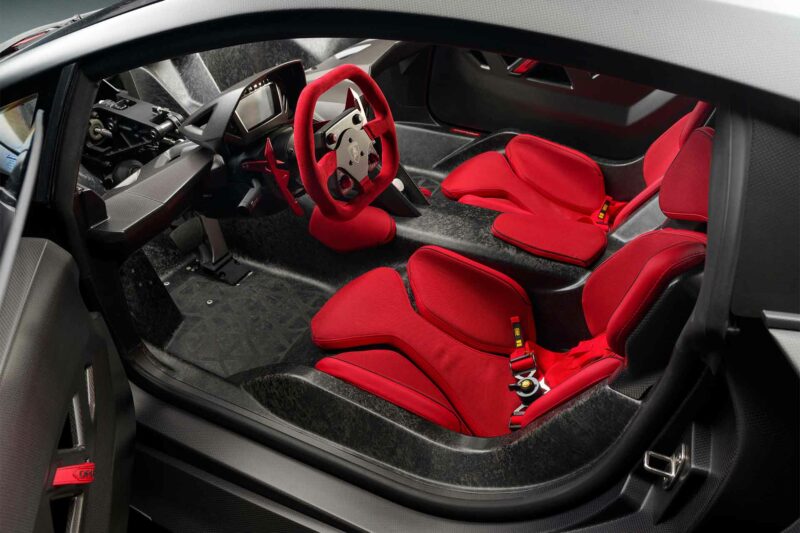
Carbon Fiber Basics
Let’s go through what carbon fiber is and why it has exceptional properties. You’ll soon see why it is such a good fit for supercars.
What is carbon fiber made from?
Carbon fiber is a composite material, meaning it combines materials. Carbon fiber composite suspends carbon fibers in the middle of a polymer. The polymer allows the composite to hold a shape while the carbon fibers add strength and rigidity.
Carbon fiber is not a metal; it is closer to plastic. The polymer part of carbon fiber composite is plastic. However, the addition of carbon fibers makes the material far more robust than plastic alone.
Carbon Fibers
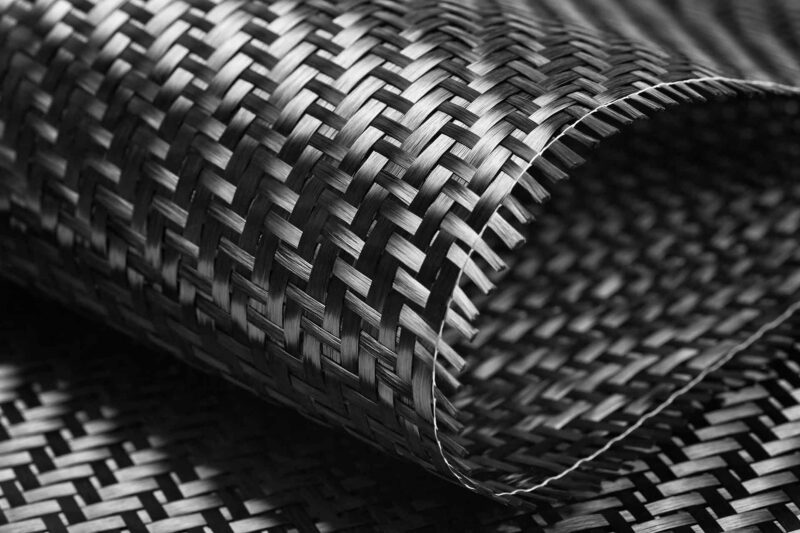
Carbon fibers are very thin strands of carbon atoms. These strands are often less than ten micrometers wide.
The fibers are carbon atoms bonded in a crystal alignment parallel to the fiber’s length. These molecular bonds give the fibers exceptional tensile strength. Imagine pulling on both ends of a rope; the tensile strength is the maximum force the rope can handle before it stretches or snaps.
These carbon fibers are woven in sheets, with the strands pointing in different directions to give strength in all directions.
Patterns of carbon fiber weaves:
- Plain Weave
- Twill Weave
- Harness Satin Weave
- Fish Weave
- Spread Tow
- Braids
- Unidirectional Weave
- Custom Weaves
The weave you will recognize on supercars is the twill weave. Learn more about the differences between the weaves in this article on the Dragon Plate website.
Polymer
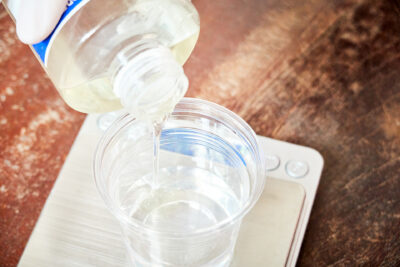
Polymers in carbon fiber composite materials serve as the binding substance that encases and supports the carbon fibers. Engineers call it the matrix material.
Basically, the polymer glues a sheet of carbon fiber cloth into a shape. The carbon fiber strands are also glued to each other, giving them collective strength.
These polymers, typically epoxy, act as a glue that holds the carbon fibers together, forming a solid structure. This combination grants high strength and stiffness of the carbon fibers with the ability to hold a shape and compressive strength of the polymer.
The polymer matrix also protects the carbon fibers from environmental damage and impact. It also distributes stress across the material, ensuring that the carbon fibers can effectively carry loads without failing.
Types of Carbon Fiber Construction
There are many ways carbon fiber is made.
All methods include the following steps:
- placing carbon fibers in a mold
- adding a polymer resin
- push the resin to flow around the carbon fibers and displace any air
- curing the resin with heat or a chemical hardener
Carbon fiber construction methods include:
Prepreg Carbon Fiber
Prepreg carbon fiber construction involves using pre-impregnated carbon fibers with a resin matrix, meaning the fibers are already coated with resin before molding. Prepreg materials are laid into a mold in the desired shape. The mold is then heated and pressurized to cure the resin, which hardens the material into its final form.
This method allows for precise control over the resin-to-fiber ratio and uniform resin distribution, resulting in a high-quality, consistent composite.
Resin Infusion
Resin infusion is a method of making carbon fiber parts where dry carbon fiber layers are placed into a mold and then infused with resin.
The mold containing the carbon fibers is sealed with a plastic bag, and a vacuum is applied. The vacuum draws liquid resin into the mold, going on and around all the carbon fibers. Then, the resin is left to cure, hardening into its final shape.
Resin infusion is used to create parts with complicated 3D shapes.
Lamborghini specializes in resin infusion to make the carbon fiber parts for their supercars.
Wet Layup
The wet layup method for making carbon fiber parts involves manually applying a liquid resin to layers of carbon fiber cloth laid out in a mold.
The carbon fiber cloth is placed into the mold, then resin is brushed or rolled onto it, which saturates the fibers. Multiple layers can be added depending on the desired thickness and strength.
The composite is left to cure into its final shape in an oven or at room temperature with a hardener.
This method is relatively simple and cost-effective, making it suitable for small-scale or custom carbon fiber part production. It is similar to old-school fiberglass construction. You could make a carbon fiber hood in your garage with a wet layup process.
However, wet layup is less efficient, predictable, and precise than other construction methods to make carbon fiber. Engineers know it leaves excess resin that makes the part thicker and heavier without contributing to its strength. There are better choices for supercars.
Forged Carbon Fiber
Forged carbon fiber parts are made by mixing chopped carbon fiber strands with a resin and applying pressure to squeeze out the air and excess polymer.
Forged carbon fiber parts have a unique marbled appearance, which is different from the woven pattern of a typical carbon fiber part.
Forged carbon fiber allows for more complex shapes and designs. This method is often used for producing solid and lightweight components with complex geometries to do a specific job.
Lamborghini and Callaway (the golf equipment company) worked together to research forged carbon fiber construction to create a material they call “Forged Composite.” Lamborghini used forged composite for the first time in the Sesto Elemento in 2013, and Callaway used it in their high-end drivers, fairway woods, and hybrid clubs ever since.
Properties of Carbon Fiber
Carbon fiber has unique properties compared to conventional materials, so mechanical engineers spec CF for unique uses like in high-performance cars and motorsports.
High Strength
Carbon fiber is very strong, particularly its high tensile strength and stiffness. This strength comes from the strong carbon bonding between atoms along the carbon fibers.
The carbon fibers in CFRP provide substantial resistance to stretching or pulling forces (i.e., tensile strength). Carbon fiber also has good stiffness or rigidity; it doesn’t deform under load.
Carbon fiber exhibits excellent fatigue resistance, maintaining its strength over repeated stress cycles without wear or degradation.
Carbon fiber has all of this strength with minimal weight. The combination of excellent tensile strength, stiffness, and fatigue resistance with a low weight makes it ideal for frames and bodywork of supercars and hypercars. The strength helps a car’s handling, and the low weight improves acceleration, braking, and cornering.
Is carbon fiber stronger than steel? Carbon fiber composite offers superior strength-to-weight ratio and tensile strength compared to steel. But steel has better compressive strength and is cheaper to produce. The choice between the two materials depends on the requirements of the job.
Lightweight
Carbon fiber is light, but it is not much lighter than aluminum. Carbon fiber reinforced polymer (CFRP) has a density of 2.0 g/cm3, while aluminum has a density of 2.7 g/cm3.
However, carbon fiber’s exceptional strength-to-weight ratio allows engineers to design parts with the same or greater strength with less material. In other words, parts made of aluminum or plastic need to be bulky and thick to achieve the required strength, while carbon fiber parts can be thin and light.
For example, I am an industrial designer who designed injection molded plastic parts. I have to make the plastic thick and add a lot of ribs, gussets, and braces because plastics are not very strong. If I could design them out of carbon fiber, they would be lighter because I could design the part with thinner walls and wouldn’t need all the structural features. The result is a lighter part that is just as strong.
This weight reduction is crucial in industries such as aerospace and automotive, where every ounce matters for acceleration and fuel efficiency.
For example, in the automotive industry, using CFRP for parts like frames, panels, or suspension components can significantly decrease the overall weight of a vehicle. This reduction leads to improved acceleration, handling, and fuel economy.
In essence, the strength-to-weight ratio of CFRP allows mechanical engineers to design lighter components without compromising on strength.
Thermal Resistance
Carbon Fiber Reinforced Polymer (CFRP) is thermally resistant, making it a suitable material for environments with a wide range of temperatures, like the engine bay of a supercar.
This thermal resistance means that CFRP maintains its structural integrity and mechanical properties across a wide range of temperatures. Unlike metals like steel or aluminum, which can expand or weaken significantly when heated, CFRP experiences minimal thermal expansion and retains its shape and strength even under temperature fluctuations.
This stability is particularly beneficial in industries such as aerospace and automotive, where materials are routinely exposed to high temperatures and require consistent performance.
Moisture Resistant
Carbon fiber is highly resistant to moisture, a useful property in wet or humid environments. Supercars with carbon fiber components can be driven in rain or humid air without any worry about the parts degrading.
Moisture resistance means a material will keep its strength and attributes even when wet. Imagine cardboard getting wet; it loses all its strength and gets soft and easily torn. Carbon fiber can be wet all day and stay strong.
Water doesn’t affect carbon fiber in the long term. Unlike metals that can corrode or rust when exposed to moisture, carbon fiber reinforced polymer (CFRP) remains unaffected, retaining its structural integrity and mechanical properties.
This moisture resistance is due to the polymer matrix that encases the carbon fibers, creating a barrier that prevents water absorption. This feature is precious in applications such as marine vehicles, outdoor sporting equipment, and automotive components, where designers can expect everyday interactions with water.
The ability of CFRP to resist moisture-related degradation ensures the longevity and reliability of carbon fiber components, even in damp conditions.
Expensive Per Part
Carbon fiber is expensive to manufacture, so you only see it on high-end sports cars, supercars, hypercars, and race cars. Carbon fiber is expensive and limited for a few reasons:
- The raw materials, particularly the high-quality carbon fibers, are costly because they require a precursor material, polyacrylonitrile, which needs to be transformed into carbon fibers in a specialized process.
- The manufacturing process of CFRP components is labor-intensive and time-consuming.
- The carbon fiber composite curing process requires specialized equipment like autoclaves, which are expensive to operate.
- Carbon fiber parts cure slowly, so machines and operators can only produce a few parts a day versus steel or plastic tooling, which can produce hundreds to thousands of parts.
Carbon fiber is only seen on limited, performance vehicles because carbon fiber is expensive to produce, and factories can only produce a few parts per day. The benefits of reduced weight and increased strength have to justify the cost, such as in performance parts for sports cars and supercars.
Low Tooling Cost
Fortunately, the tooling to make carbon fiber parts is relatively inexpensive and easy to make. When car companies make sheet metal fenders, they have to spend hundreds of thousands of dollars to make a tool to stamp it out, so they need to make and sell thousands of cars to pay off the expense.
When a supercar manufacturer like Lamborghini or Pagani makes a carbon fiber fender, the tooling only costs a few thousand dollars, so they only need to sell a few cars to pay for the tooling.
The relatively low tooling cost is why we have seen limited-run hypercars where they only produce twenty or so cars. Lamborghini only made one each of the Invencible and Auténtica, both made of carbon fiber. Since custom parts can be made without expensive tooling, manufacturers can make only a few parts and afford to break the mold after that.
The tooling cost of carbon fiber is so low that you could make a one-off carbon fiber component in your garage. The Easy Composites YouTube channel has excellent tutorials on making carbon fiber parts using various methods: prepreg, forged carbon, etc.
Glossary of Carbon Fiber Terms
Autoclave
An industrial appliance that creates heat and air pressure in a chamber to cure and set carbon fiber components.
Carbon Fiber
Thin strands of carbon atoms, tightly bonded in crystal alignment, are known for high stiffness, tensile strength, and low weight.
Carbon Fiber Cloth
The piece of carbon fiber weave is placed in a mold before the polymer is injected. Carbon fiber cloth comes covered in a binding agent or prepreg polymer.
Carbon Fiber Reinforced Polymer (CFRP)
CFRP is a composite material consisting of carbon fiber embedded in a polymer matrix, notable for its strength-to-weight ratio.
Carbon Fiber Weave
The arrangement of carbon fibers which affects the final part’s strength and appearance; common weave patterns include plain, twill, and satin.
Carbon Fiber Fabric Weight
Carbon fiber cloth can be specified in different thicknesses and is measured in weight per area, typically g/m^2.
Curing
The process of hardening the polymer matrix in CFRP which often involves heat and pressure to set the shape and properties of the composite.
Epoxy Resin
A type of polymer used as a matrix in CFRP for binding carbon fibers, known for its high strength and chemical resistance.
Forged Carbon Fiber
Forged carbon fiber is made by pressing a mixture of resin and short carbon fiber flakes into a mold under high pressure and baked, resulting in a robust and lightweight material with a distinctive marbled appearance. Forged carbon fiber allows for more complex shapes and designs than traditional carbon fiber layup methods.
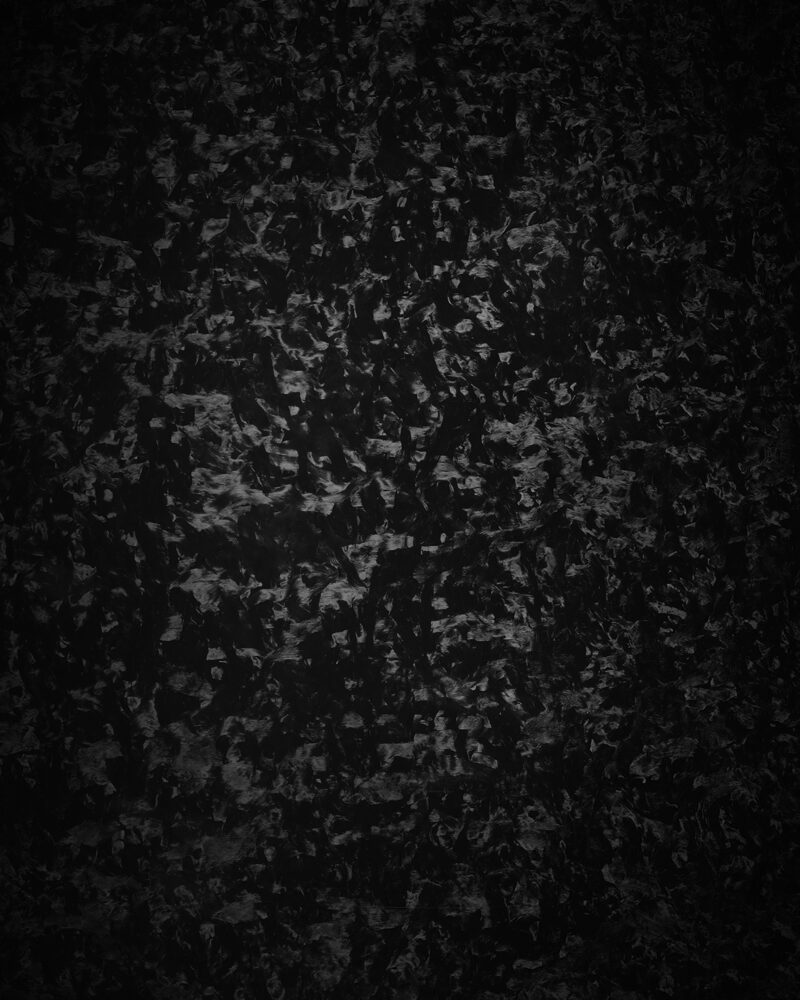
Layup
The process of layering carbon fibers and resin to create CFRP often involves manual placement of the fibers.
Prepreg Carbon Fiber
Carbon fiber weave pre-impregnated with a resin matrix in a specific ratio, ready for molding and curing.
RTM Carbon Fiber
Resin Transfer Molding is a manufacturing method where the dry carbon fiber cloth is laid into a closed mold, and the polymer is injected or sucked into the mold. RTM is a good option for parts with complex geometries and requires consistent mechanical properties.
Thermosetting Plastic
A polymer that becomes irreversibly hard upon heating, used in CFRP for the matrix material.
Acknowledgments
Thanks to Easy Composites and Dark Aero for their videos about various carbon fiber construction methods. Excellent content – go follow them! They were very helpful in helping me understand carbon fiber enough to write this piece.
Leave a Reply